The world of supplements and pharmaceuticals is one where quality and safety are paramount. In this context, Good Manufacturing Practice (GMP) certification emerges as a cornerstone, ensuring that products are consistently produced and controlled according to quality standards. This blog aims to demystify GMP certification, highlighting its significance in the supplement industry and its impact on both manufacturers and consumers. Understanding GMP is crucial for anyone involved in the production or consumption of health-related products, as it is not just a set of guidelines but a marker of trust and reliability in an industry where these qualities are non-negotiable.
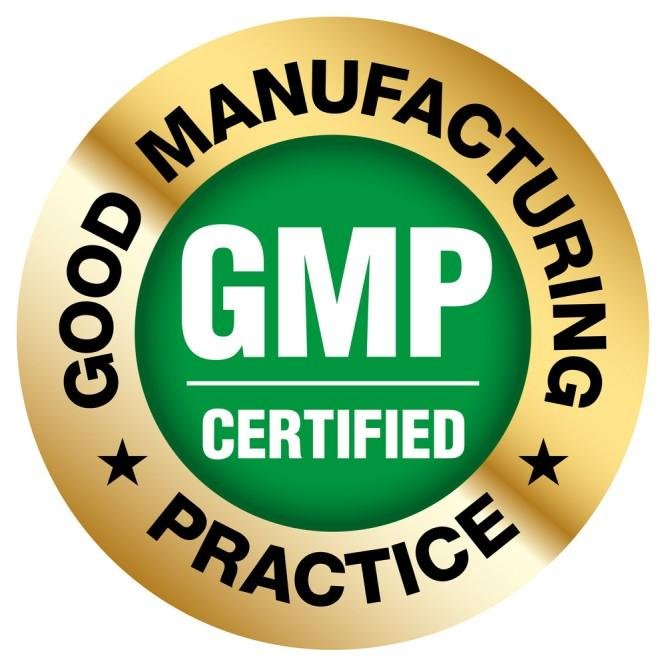
1. GMP Certification: Definition and History
1.1 Definition of GMP
Good Manufacturing Practice (GMP) refers to a system of manufacturing that guarantees the consistent production and control of products according to quality standards. It covers all aspects of production, from the raw materials, premises, and equipment to the training and personal hygiene of staff. Detailed written procedures are essential for each process that could affect the quality of the finished product. There must be systems to provide documented proof that correct procedures are consistently followed at each step in the manufacturing process.
1.2 Historical Background
The concept of GMP originated in the United States, following a tragic incident in the 1930s where a toxic solvent used in an elixir resulted in over a hundred deaths. This led to the enactment of the Federal Food, Drug, and Cosmetic Act of 1938, which required drugs to be proven safe before selling. However, it wasn't until the 1960s, following the thalidomide disaster, that the need for quality control in manufacturing processes became evident, leading to the development of GMP guidelines.
The evolution of GMP has been a response to various health hazards and manufacturing malpractices. Over the years, these guidelines have been refined and adopted globally, with many countries developing their own GMP standards, often based on the World Health Organization's (WHO) version. The implementation of GMP has significantly evolved from its initial stages, now encompassing a wide range of industries and constantly adapting to new challenges and technological advancements in manufacturing.
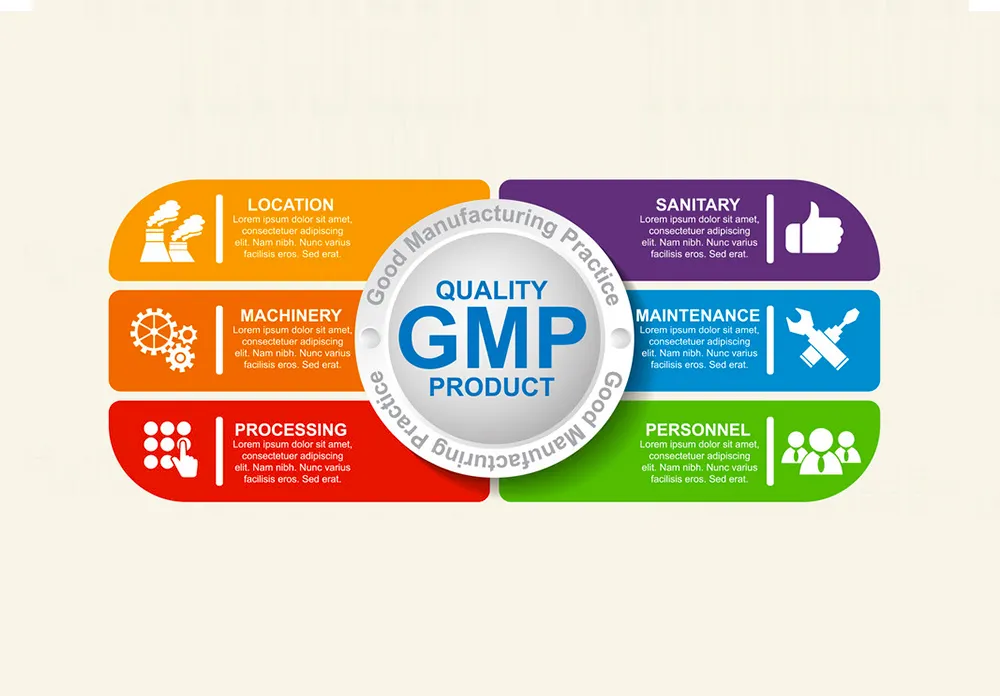
2. GMP Certification: Standards and Requirements
2.1 Core Standards of GMP
The standards of Good Manufacturing Practice (GMP) are designed to ensure that products are consistently produced and controlled according to quality standards. These standards encompass several key areas:
- Quality Management: This involves ensuring that all manufacturing processes are defined, systematically reviewed, and shown to be capable of consistently manufacturing pharmaceutical products of the required quality.
- Personnel: Adequate numbers of qualified personnel must be employed, with clear responsibilities and training. This includes ongoing training programs and hygiene standards for all staff involved in the manufacturing process.
- Premises and Equipment: The manufacturing facility must be appropriately designed and maintained, with suitable equipment that is regularly calibrated and maintained. This includes ensuring a clean and hygienic manufacturing area and controlled environmental conditions to prevent cross-contamination.
- Documentation and Records: Accurate and detailed documentation is crucial. This includes the formulation, processing, packaging, and quality control procedures. Records must be kept for every batch produced, demonstrating compliance with the GMP standards.
- Production: Production operations must follow clearly defined procedures, with all necessary controls in place. This includes managing critical processes and potential risks to product quality.
- Quality Control: There must be a comprehensive system for sampling, testing, and documentation of raw materials, packaging materials, and finished products to ensure they meet specified standards.
2.2 Requirements for GMP Certification
To achieve GMP certification, a facility must demonstrate a robust quality management system, compliance with hygiene standards, adequate premises and equipment, and effective procedures for production and quality control. The facility must also show it can consistently produce products meeting the required quality standards and that it has the capability to recall any batch of product from sale or supply.
3. The Process of Obtaining GMP Certification: A Case Study on Gummy Supplements
Obtaining Good Manufacturing Practice (GMP) certification for supplement products, such as gummy vitamins, involves a detailed and rigorous process. This process ensures that the products are manufactured consistently and with quality. Here's an illustrative case study outlining the steps a gummy supplement manufacturer might take to obtain GMP certification.
3.1 Initial Assessment and Preparation
- Gap Analysis: The manufacturer begins with a comprehensive gap analysis to assess current practices against GMP standards. This includes evaluating procedures, equipment, personnel training, and quality control measures specifically for gummy supplement production.
- Implementation of GMP Protocols: Based on the gap analysis, the company implements necessary changes. For gummy supplements, this might include upgrading equipment to ensure precise ingredient mixing, temperature control during the gelling process, and contamination-free packaging lines.
3.2 Steps Towards Certification
- Documentation and System Establishment: The company develops detailed documentation of all processes, from sourcing raw materials to final product testing. This includes establishing traceability systems for ingredients, particularly for critical components like gelatin or pectin, flavorings, and colorings.
- Staff Training: Employees receive training on GMP standards, focusing on areas critical to gummy supplement production, such as maintaining hygiene standards in the mixing and molding areas.
- Facility Upgrade: If necessary, the facility is upgraded to comply with GMP standards. This might involve redesigning the production area to prevent cross-contamination and ensure a controlled environment for the sensitive gelling and curing stages of gummy production.
3.3 The Certification Process
- Application for Certification: The manufacturer applies for GMP certification with a relevant authority or third-party auditor, providing detailed documentation of their processes and quality control measures.
- Pre-Audit Assessment (Optional): The company may opt for a pre-audit assessment to identify any potential compliance issues, particularly those unique to gummy supplement manufacturing.
- Formal Audit: A thorough audit is conducted, examining every aspect of the gummy supplement production process. This includes verifying the quality of raw materials, the efficiency and cleanliness of the equipment, and the training and competence of the staff.
- Addressing Audit Findings: If the audit identifies areas of non-compliance, the manufacturer must promptly address these issues. This could involve further refining the production process or enhancing quality control measures.
- Receiving Certification: Once all GMP standards are met and any issues resolved, the manufacturer receives GMP certification, affirming their commitment to producing high-quality, safe gummy supplements.
3.4 Maintaining Certification
GMP certification requires ongoing compliance. The manufacturer must continually monitor and improve their processes, conduct regular internal audits, and be prepared for periodic re-audits by the certifying body to maintain their GMP certification status.
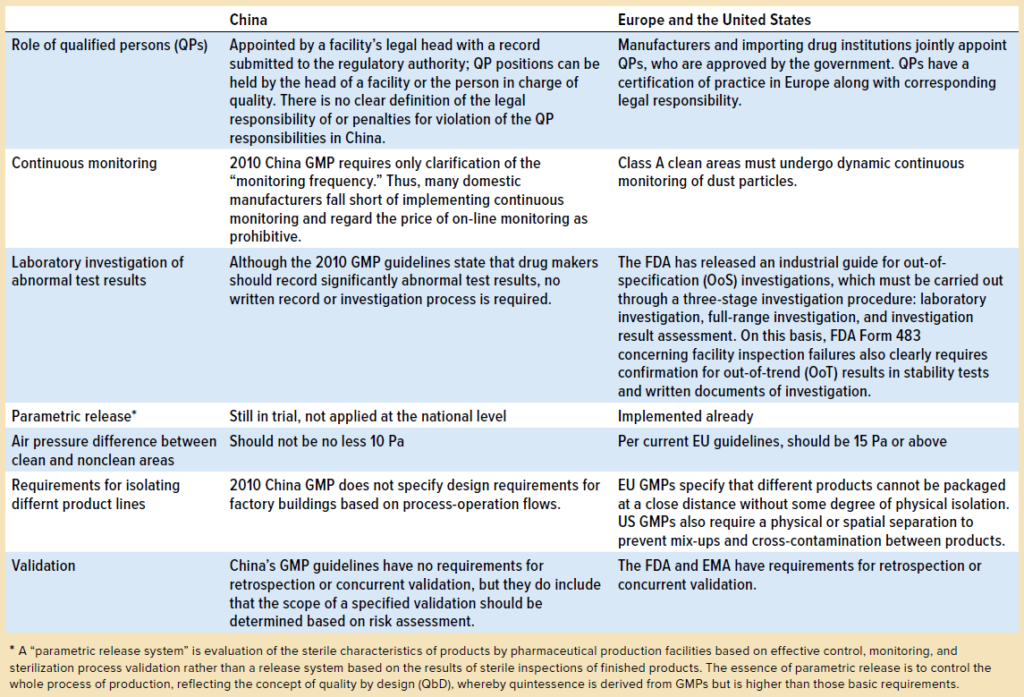
4. GMP Compared to Other Quality Certifications: ISO, HACCP, and FDA
Understanding the distinctions between various quality certifications is crucial for businesses in the supplement and food industries. Here, we compare Good Manufacturing Practice (GMP) with ISO standards, Hazard Analysis Critical Control Point (HACCP), and FDA regulations, highlighting their unique features and applicability.
4.1 GMP vs. ISO Standard
A. Scope and Focus:
- GMP: Primarily focuses on manufacturing processes, ensuring products are consistently produced and controlled according to quality standards. It's more prescriptive about the manufacturing process.
- ISO (e.g., ISO 9001): ISO standards, such as ISO 9001, are broader in scope, focusing on overall quality management systems. They are more about ensuring a process for quality management rather than specific manufacturing guidelines.
B. Application
- GMP: More specific to the pharmaceutical, cosmetic, and food industries, including supplement manufacturing.
- ISO: Applicable to a wide range of industries, not limited to health and food sectors.
4.2 GMP vs. HACCP
A. Focus Area:
- GMP: Emphasizes consistent quality in manufacturing processes, including cleanliness, record-keeping, and personnel qualifications.
- HACCP: Focuses on identifying and preventing hazards that could cause food to be unsafe, covering biological, chemical, and physical hazards.
B. Implementation
- GMP: Involves detailed guidelines for every aspect of production, processing, and packaging.
- HACCP: More about analyzing and controlling hazards at specific points in the process.
4.3 GMP vs. FDA Regulations
A. Regulatory vs. Certification:
- GMP: A certification that demonstrates compliance with specific manufacturing practices.
- FDA Regulations: Legal requirements set by the U.S. Food and Drug Administration. Compliance with FDA regulations is mandatory for products sold in the U.S., including food, drugs, and dietary supplements.
B. Scope
- GMP: Part of FDA regulations but specifically focused on the manufacturing process, ensuring products are made safely and consistently.
- FDA Regulations: Cover a broader range of aspects, including product labeling, safety testing, and marketing claims.
In summary, GMP is essential for companies that want to ensure their manufacturing processes meet industry-specific quality standards.
ISO certifications are suitable for organizations looking to implement a comprehensive quality management system across various departments and processes.
HACCP is critical for businesses in the food industry, focusing on food safety through hazard control.
Compliance with FDA Regulations is mandatory for products in the U.S. market and includes adherence to GMP as part of its broader regulatory framework.
Each of these certifications and regulations serves a unique purpose, and businesses may seek one or more of these certifications depending on their industry, product type, and market requirements.
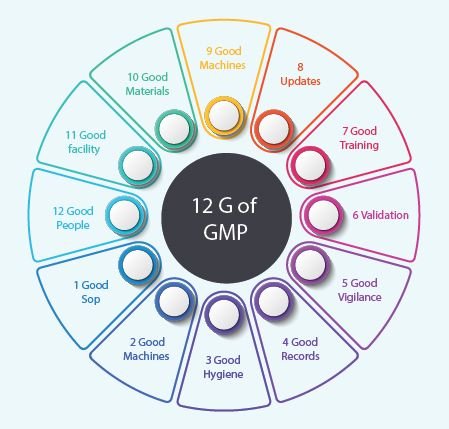
5. GMP Certification: Implications for Consumers
Understanding the Consumer Perspective
5.1 Assurance of Quality and Safety:
GMP certification provides consumers with the assurance that the products they purchase are manufactured under stringent quality control standards. This is particularly vital in industries like pharmaceuticals, supplements, and food, where quality directly impacts health and safety
A. Informed Choices
- With GMP certification, consumers can make more informed decisions. Knowing that a product is GMP certified helps in distinguishing between products that meet high manufacturing standards and those that may not.
B. Trust in Brands
- Products with GMP certification often earn greater trust from consumers. This trust is built on the understanding that the manufacturer is committed to maintaining high-quality production standards.
C. Reduced Risk of Product Recalls and Health Hazards
- GMP-certified products are less likely to face recalls due to quality issues. This reduces the risk of health hazards associated with poorly manufactured products.
5.2 GMP Certification: Impact on Manufacturers
Navigating the Manufacturer's Landscape
A. Enhanced Credibility and Market Access
- Obtaining GMP certification can significantly enhance a manufacturer's credibility. It often becomes a prerequisite for entering certain markets, especially in the pharmaceutical and food industries.
B. Improved Product Quality
- The process of achieving GMP certification necessitates a thorough review and improvement of manufacturing processes. This leads to higher product quality and consistency.
C. Increased Efficiency and Reduced Waste
- Implementing GMP standards often results in more efficient manufacturing processes. By standardizing procedures and reducing errors, manufacturers can decrease waste and increase productivity.
D. Compliance and Legal Benefits
- GMP certification helps manufacturers stay compliant with national and international regulations, reducing the risk of legal issues and penalties associated with non-compliance.
E.Competitive Advantage
- In a market where consumers are increasingly aware of manufacturing standards, GMP certification can provide a competitive edge. It differentiates a manufacturer's products from those of competitors who may not have similar certifications.
F. Cost Implications
- While obtaining and maintaining GMP certification involves initial and ongoing costs, the long-term benefits often outweigh these expenses. Improved product quality and market reputation can lead to increased sales and customer loyalty.
In conclusion, GMP certification plays a pivotal role in ensuring product quality and safety, benefiting both consumers and manufacturers. For consumers, it offers assurance and trust in the products they use. For manufacturers, it not only enhances credibility and market access but also drives improvements in manufacturing efficiency and product quality.
6. Global Perspectives on GMP Certification
6.1 Navigating GMP Standards Across Different Regions
A. GMP in China:
- Regulatory Framework: In China, the China Food and Drug Administration (CFDA) oversees GMP standards. The Chinese GMP standards have evolved significantly, aligning more closely with international norms.
- Implementation: Chinese GMP standards are stringent, focusing on quality management, personnel, premises, and documentation. Recent updates have emphasized risk management and quality control throughout the manufacturing process.
- Challenges and Progress: While compliance has been challenging for some local manufacturers, there has been a notable shift towards higher quality standards, driven by both regulatory pressures and market demands.
B. GMP in North America (USA and Canada):
- Regulatory Bodies: In the USA, the Food and Drug Administration (FDA) sets GMP standards, known as cGMP (current Good Manufacturing Practices). In Canada, Health Canada is the regulatory authority.
- Key Features: North American GMP standards are among the most rigorous globally. They emphasize not just compliance but also continuous improvement in manufacturing processes.
- Industry Impact: The FDA and Health Canada regularly inspect facilities and enforce compliance, ensuring high standards in pharmaceuticals, dietary supplements, and food products.
C. GMP in Europe:
- EU Regulations: The European Medicines Agency (EMA) and individual country regulatory agencies oversee GMP standards in Europe. The EU GMP guidelines are comprehensive, covering all aspects of production and quality control.
- Harmonization Efforts: Europe has been at the forefront of efforts to harmonize GMP standards internationally. The EU GMP guidelines have served as a benchmark for many countries developing their own standards.
- Cross-Border Implications: For manufacturers, meeting EU GMP standards is crucial for market access across Europe. The EU's mutual recognition agreements with other countries also extend the impact of its GMP standards globally.
6.2 Comparative Analysis
While there are regional differences in GMP standards and enforcement, the core principles remain consistent: ensuring product quality, safety, and efficacy.
In China, the focus has been on aligning local standards with international norms, whereas North America emphasizes continuous improvement and stringent enforcement. Europe, on the other hand, plays a key role in international harmonization of GMP standards.
Manufacturers aiming for global market access must navigate these regional variations, often adhering to the most stringent standards to ensure compliance across different markets.
In summary, understanding the nuances of GMP certification in different regions is crucial for manufacturers operating on a global scale. While the fundamental goal of GMP—to ensure product quality and safety—is universal, the specific standards and regulatory approaches can vary significantly from one region to another,
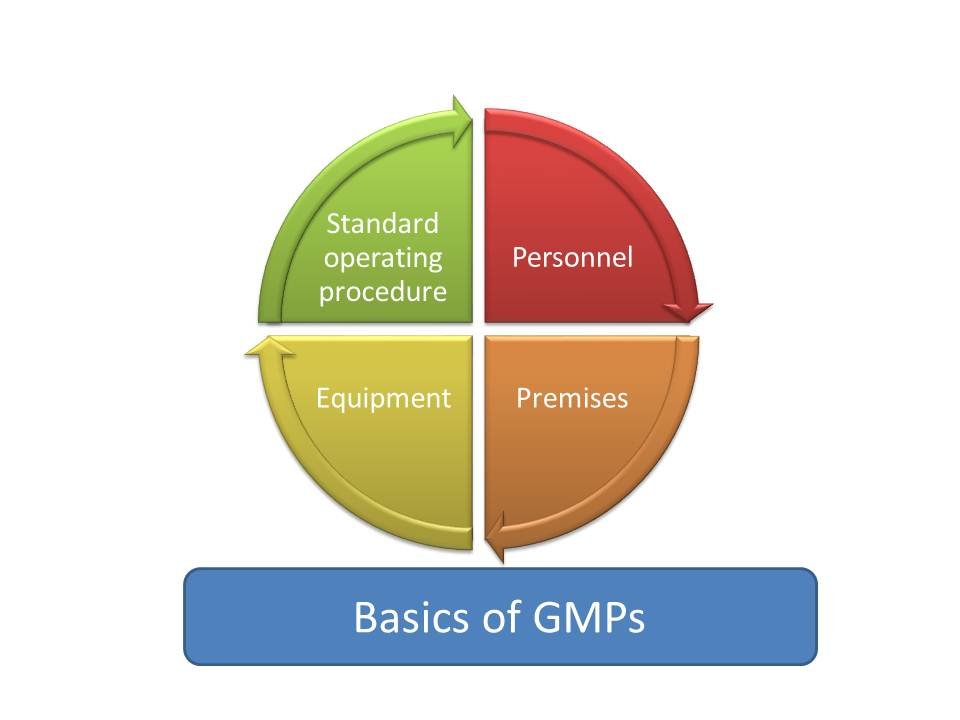
7. Future Trends and Challenges in GMP Certification
Adapting to Evolving Standards and Global Challenge
7.1 Technological Advancements
- Automation and AI: The increasing use of automation and artificial intelligence in manufacturing processes presents both opportunities and challenges for GMP compliance. These technologies can enhance precision and consistency but also require updated regulatory frameworks.
- Data Integrity: With digital systems becoming integral to manufacturing, ensuring data integrity is paramount. This includes secure data storage, accurate record-keeping, and protection against cyber threats.
7.2 Globalization and Supply Chain Complexity
- International Supply Chains: As supply chains become more globalized, ensuring GMP compliance across different countries and suppliers becomes more complex. This requires robust systems for supplier qualification and audit.
- Regulatory Harmonization: There is a growing need for international regulatory harmonization to simplify compliance for companies operating in multiple markets. Efforts by organizations like the International Council for Harmonisation of Technical Requirements for Pharmaceuticals for Human Use (ICH) are crucial in this regard.
7.3 Emerging Markets and Regulatory Development
- Growth in Emerging Markets: Emerging markets are playing an increasingly significant role in the global pharmaceutical and supplement industry. Adapting GMP standards to these new markets, while ensuring quality, is a key challenge.
- Evolving Regulations: Regulatory bodies worldwide are continuously updating GMP standards to reflect new scientific knowledge and manufacturing practices. Keeping up with these changes is essential for manufacturers.
7.4 Sustainability and Ethical Considerations
- Environmental Impact: There is a growing emphasis on the environmental impact of manufacturing processes. Integrating sustainable practices with GMP compliance is becoming increasingly important.
- Ethical Manufacturing: Ethical considerations, including labor practices and sourcing ethics, are becoming integral to GMP. Consumers and regulators are paying more attention to these aspects.
8. Conclusion
The landscape of Good Manufacturing Practices (GMP) is continually evolving, shaped by technological advancements, globalization, and changing regulatory environments. As manufacturers strive to maintain compliance, they must also adapt to emerging trends and challenges, including the integration of new technologies, managing complex global supply chains, and responding to the growing demands for sustainability and ethical manufacturing.
Navigating these changes requires a proactive approach, with an emphasis on continuous learning, adaptability, and collaboration with regulatory bodies and industry partners. By staying ahead of these trends, manufacturers can not only ensure compliance with current GMP standards but also position themselves for success in a rapidly changing global market.
In conclusion, GMP certification is not just about meeting regulatory requirements; it's about embracing a culture of quality, safety, and continuous improvement. As the industry moves forward, those who adapt and innovate will be best positioned to meet the demands of a dynamic global marketplace, ensuring the highest standards of product quality and consumer safety.
References:
One Response